Can 3D printing solve labour shortages while improving sustainability in maritime, offshore or logistics?
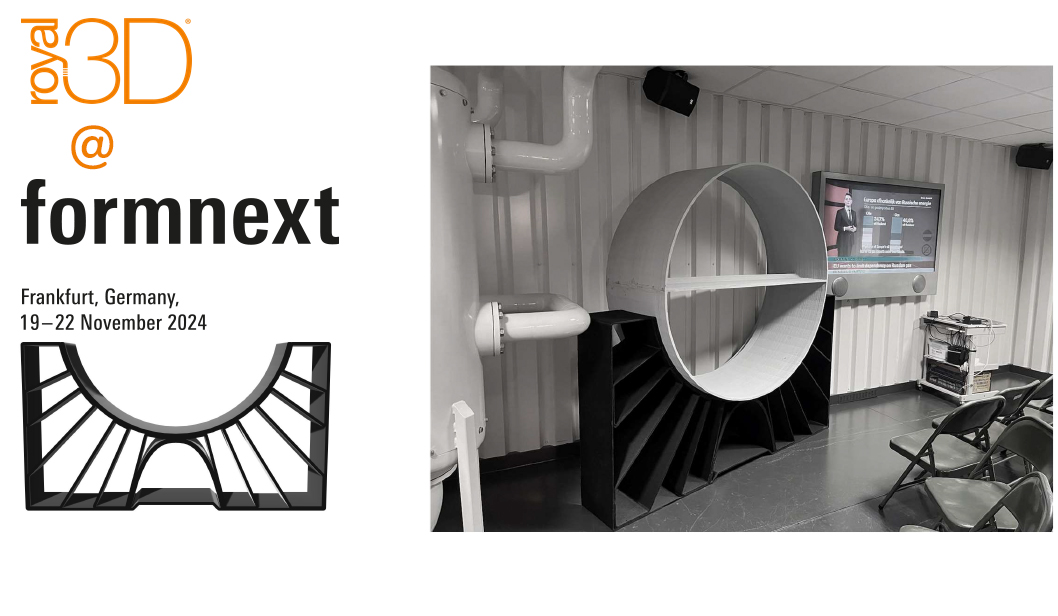
Column by Bob de Reus, Industrial designer at Royal3D:
On 20 and 21st of November, I’ll be representing Royal3D at the FORMNEXT 2024 fair in Frankfurt, the world’s leading event for additive manufacturing and industrial 3D printing. This event is the perfect opportunity to showcase how large-scale 3D printing can tackle two pressing challenges in industries like maritime, offshore and logistics: labour shortages and sustainability. Imagine reducing the reliance on hard-to-find skilled labour while simultaneously cutting costs and environmental impact. Let’s explore what I’ll discuss at FORMNEXT and what 3D printing is truly capable of in addressing these challenges.
Why large-scale 3D printing is a game changer
At Royal3D, we specialize in printing large-scale items, from molds and boats to support cradles for monopiles and wind turbine blades. These aren’t just big; they’re innovative in every sense. Traditional methods, like wooden support cradles or aluminum molds, are costly, wasteful, and time intensive. For example, a typical mold for e.g. an entire boat, yacht component of industrial casings can cost tens of thousands of euros and take much time to fabricate. A 3D-printed alternative costs so much less, or better yet, you can skip the mold entirely and print the product directly.
Pushing sustainability to the limit with 3D printing
Cost isn’t the only factor to consider. For example, wooden support cradles used for transportation of odd-shaped goods are typically discarded after use, contributing to unnecessary waste. In contrast, our support cradles are crafted from durable, recyclable plastics that can be reused and reprinted multiple times. This closed-loop process not only minimizes environmental impact but also lowers material costs with each cycle, making it a solution that’s both sustainable and economically intelligent.
3D printing: Tackling labour shortages while improving efficiency
Labour shortages are a growing challenge, especially in industries like maritime and wind energy. Take the production of support cradles as an example currently, manufacturing these cradles requires significant manual labour, often amounting to dozens of man-hours for a single large cradle. This reliance on intensive labour not only slows down production but also strains resources in a sector already struggling with workforce availability. With 3D printing, this process can be fully automated, eliminating the need for manual fabrication and allowing those hours to be redirected toward more specialized tasks. This improves efficiency and addresses the labour shortage head-on.
A unique approach to collaboration
What sets us apart at Royal3D is our ability to print items as large as 4x4x8 meters and recycle materials in-house. But more importantly, we believe in working closely with our customers. Developing large-scale printed products can feel daunting if you’ve never done it before, so we offer one-on-one guidance throughout the process. From the initial concept to final production, we ensure you’re supported every step of the way.
Many companies are surprised to learn how easily 3D printing can match or even surpass traditional materials and methods. Take support cradles as an example. Our 3D-printed designs don’t just replace wood and steel; they fit better, often perform better, and are ways more sustainable.
Pushing the boundaries of what’s possible
We’re constantly refining our technology to meet the demands of large-scale printing. Right now, we’re focusing on optimize strength and layer adhesion by monitoring and controlling temperature during the printing process. These improvements help us create even stronger and more reliable products.
At FORMNEXT 2024, I’m particularly interested in exchanging ideas with other experts. What challenges are they facing with large-scale 3D printing? How are they advancing material performance or finding new applications? These conversations are invaluable, not just for pushing technology forward but also for discovering new ways it can benefit industries.
The big 3Dprinting picture
The potential of large-scale 3D printing is vast, especially in industries like maritime. Take support cradles, for example. Our 3D-printed designs are not only lighter and more sustainable than traditional materials, but they're also fully customizable to fit the unique contours of monopiles and wind turbine blades—something that’s challenging to achieve with wood or steel. This level of precision and adaptability opens new possibilities for efficiency and innovation.
What does this mean for you?
At FORMNEXT, I’m excited to explore how 3D printing can transform your operations. Whether you're looking to cut costs, tackle labour shortages, or achieve your sustainability goals, large-scale 3D printing offers solutions that can reshape how you do business. So, let me ask: What if your next product could be produced faster, more cost-effectively, and with a significantly lower environmental impact—thanks to 3D printing?
Let’s connect at FORMNEXT to discuss how this technology can drive your projects forward, enhance sustainability, and help address workforce challenges.